When Habitat28 was founded in 2022, CEO Shailesh Poddar wanted to make a difference in the way people live by designing and building homes that were affordable and sustainable.
Poddar, who has a career in construction spanning over 33 years, has utilized his skills, extensive experience, and entrepreneurial background to create an organization that is focused on designing homes that fully suit the needs of each customer.
He learned about the budding self-contained and pre-fabricated home industry in the United States.
“Up until around 2017, I was fairly happy, doing about ten custom houses a year [and] then all of a sudden, I started hearing about these companies that were opening up in Texas and other places which were building these beautiful self-contained and pre-fabricated units. They were almost like these things that you could put in your backyard and start living in them…they also could be energy efficient and it dawned upon me that the smaller construction would also be much greener,” explained Poddar. “I started exploring this [and] what I found was that while America had already started to recognize this…Canada wasn’t there yet, policy-wise. You couldn’t put much more than a 100-square-foot shed in your backyard so we were committed to working in the Canadian market to change things.”
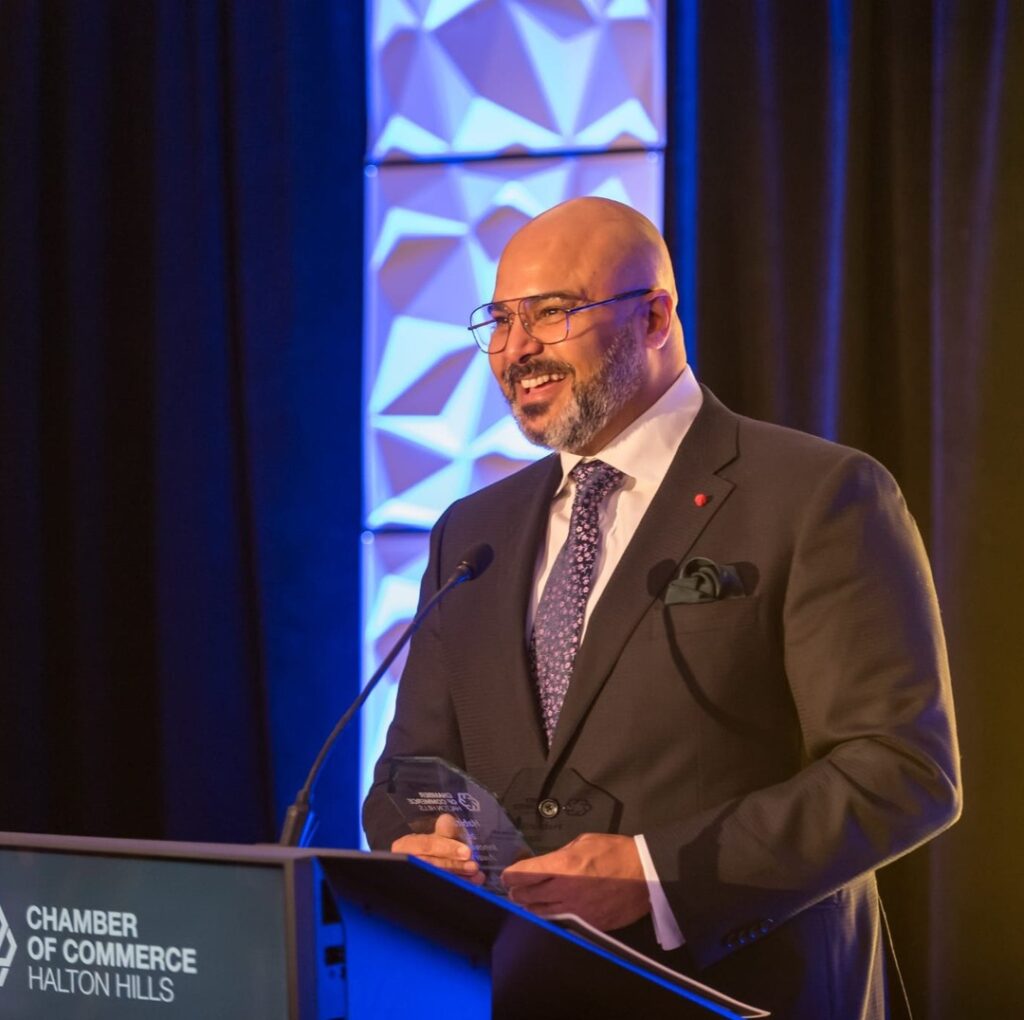
However, Poddar waited for the right time to launch Habitat28 with the looming housing crisis and sharp increase in housing prices, and spent a year educating and connecting with people about Accessory Dwelling Units (ADUs) which were separate, self-contained residential units on the same property as a primary living quarters.
“Three years ago, when Bill 23 was passed in Ontario, it changed everything. It changed the policy that would now allow for additional dwelling units or smaller houses to be put in backyards [and] to be used as residential or rental properties. We realized this was our moment [and] dove in. So that’s how we got into this industry,” explained Poddar. “[But] there was a large amount of investment that was required to be made on our part, and we wanted to make sure that we were catching the pulse and not just doing something that we thought was cool, but also people needed it. For us, the first year was all about awareness. We were at the Toronto Premium Outlets [in Halton Hill, Ontario] and had one of our units there and offices there, and we were talking to about 2,000 people a week, and we were telling them about ADUs and we were educating them on the laws that had already been passed.”
That year Poddar was also focused on what people were looking for when it came to these types of homes.
“The useability cases became extremely important which helped us shape the models and what they would need. We are currently building our fifth generation of houses, which means that generation one to four needed upgrading [and] needed to be changed. And even today, we keep talking to a lot of our clients…trying to understand how we can change [to better suit their growing] needs and requirements. So that was our initial foray, and once we knew what we were doing, we started our factory [and] we started to build. We knew that the foundation of the company had to be strong and ‘tiny homes’ was no longer only what people were asking for,” he said. “People were also asking for something modular. And we realized that over the next two to three years, modular was where it’s all going…so, we invested a lot of time and resources into getting our CSA certification, which put us head and shoulders above a lot of the other manufacturers, because it’s not that common for a lot of people to have that certification. And now we can build modular, institutional, residential and commercial up to 6,000 square feet. So that added a new range of products that we could then offer to our clients.”
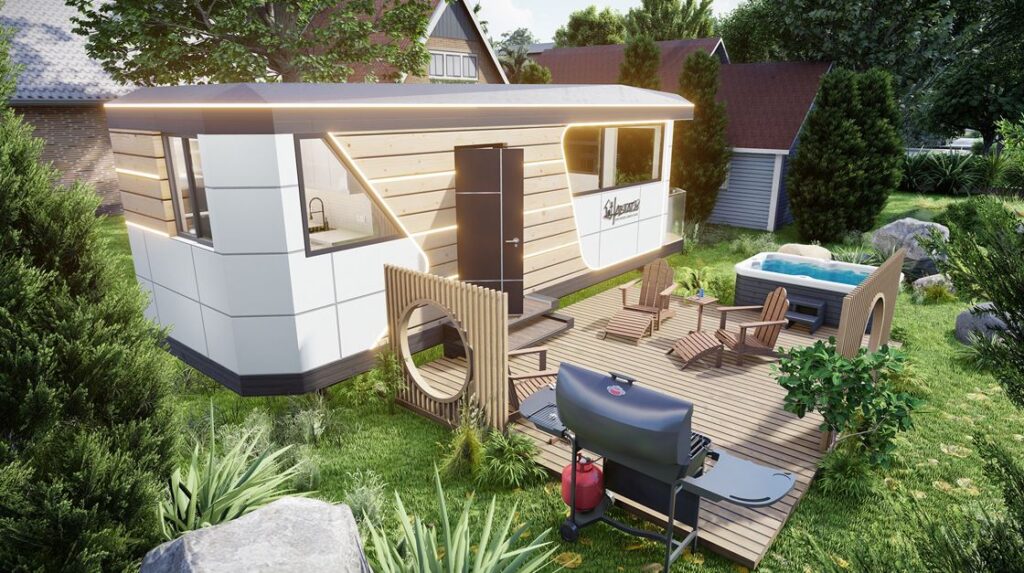
Nevertheless, for Poddar and Habitat28, the focus continues to be on the customer and learning about their unique living requirements.
“When a client comes to us, they are typically curious, and they want to know how this new concept of modular homes can help them. So first of all, we explain to them how this is designed from the beginning. So, you can’t bring a pre-designed home to us, and then we convert that into modular…a modular home has to be designed from scratch because of the way the modules have to fit together. Currently, many of our clients are seniors who are looking to either one in their backyard for their grandchildren or want one for themselves [because they want to] rent out their existing house,” Poddar said.
Poddar said the process is straightforward, pending approval from the municipality.
“We first do a digital site survey for them [and find out] …if they have enough space for [a unit] in their backyard. Generally, we try to start a conversation with the municipality and let them know that this is happening and if they are supportive of this,” said Poddar. “Once we know all of those details, then we present the client with some options that they can use, or that they can choose from. And then the designing process starts. We already have some pre-designed models. But everybody is a little bit unique [and have] different needs, so we always try to see how our modular units can be reshaped to their desired outcome.”
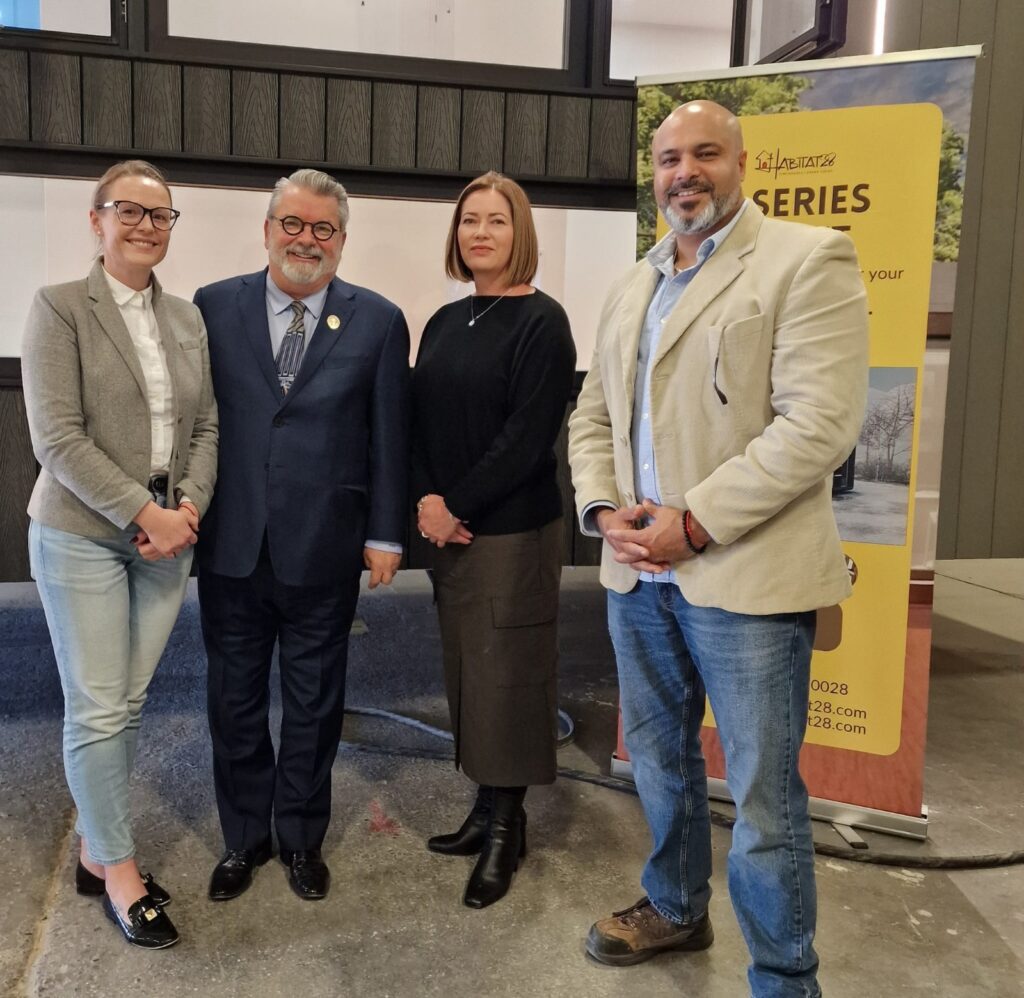
A key component to the company’s future growth was finding a suitable place to take up roots, which they discovered with Brantford and Brant County, who were welcoming.
“It was very important that where we were building…they would be a pro modular municipality [and] would be open to innovation…unfortunately, we didn’t find that support…in fact, we found a lot of resistance in several municipalities…eventually we found our way into Brantford,” he noted. “Brantford is an up-and-coming industrial city [which] has been a perfect fit for us…there was space available and talent and most importantly, our meeting with the CBO, municipal inspectors, and the building and planning department went extremely well. They are well aware of the changing face of housing [and] they were supportive.”
However, Poddar, who’s organization already boasts a collection of awards including the Sustainability Award for its innovation and dedication to building greener homes, feels that the future is now when it comes to smaller and modular homes and the importance of municipalities keeping an open mind.
“I believe we’re looking at a wonderful time for modular construction [and the] world has already moved on as Canada continues to play catch up. I believe those in power are recognizing that, and are making inroads and provisions to simplify the process. We have to cut some of the bureaucracy. I found in my research that four to six percent of all residential buildings are made inside factories as of 2020 and that by 2030 that upwards of 15% of all the buildings would be made inside factories. I’m a firm believer that off-the-shelf housing is going to be the only saving grace going forward,” he said. “What we have to do is we have to have pre-approved builders with pre-approved design templates, and this way, we cut the bottleneck at the municipal level [which] allows clients who are looking for a house to have the option of being able to either go the traditional route if they have time and resources, or choose the modular route, which means that we could literally deliver the house to them the next day…I think that’s where we are headed.”
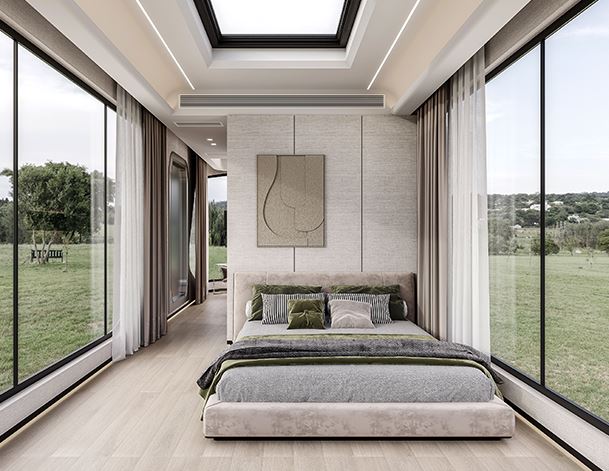